In the global textile industry, China holds a prominent position as a major producer and exporter of high – quality cotton cloth and yarn. Importing these raw materials from China can be a strategic move for businesses in the textile, garment, and related sectors. This comprehensive guide will walk you through the entire process of importing custom – made cotton cloth and yarn from China, covering all aspects from sourcing reliable suppliers to dealing with shipping, customs, and associated costs.
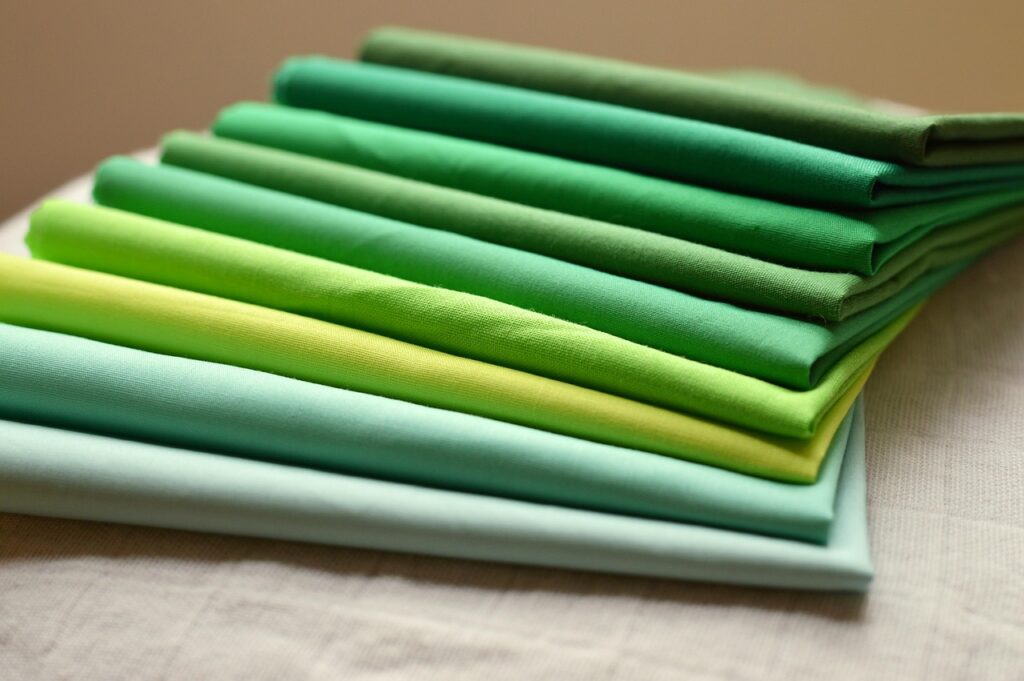
Contact us now
we are a licensed and trusted international trading company with years of experience in sourcing and fulfilling orders in China. Whether you’re looking for bulk purchases, customized products, or tailored logistics solutions, our team is dedicated to delivering transparent, reliable service.
📱 Contact Us on WhatsApp
1. Identifying Reputable Suppliers in China
1.1 Utilizing Online Business Platforms
The digital age has significantly simplified the process of connecting with Chinese suppliers. Platforms like Alibaba, Made – in – China, and Global Sources are bustling marketplaces filled with numerous textile raw material suppliers. On these platforms, importers can explore a vast range of cotton cloth and yarn products, compare prices, read customer reviews, and directly communicate with potential suppliers. Basic access to these platforms is generally free. However, for enhanced features such as more refined search filters to find suppliers with specific expertise in custom – made cotton products, priority messaging, and in – depth market reports, a paid subscription is often necessary. Subscription fees can vary widely, typically ranging from a few hundred to several thousand dollars per year, depending on the platform and the level of service. For example, Alibaba’s Gold Supplier membership, which offers increased visibility and better communication channels with suppliers, has different pricing tiers based on the type of business and the services included. This can be particularly beneficial for importers looking for high – quality custom – made cotton cloth and yarn, as it allows them to access more detailed information about the suppliers and their capabilities.
1.2 Participating in Trade Shows and Exhibitions
Attending textile and raw material trade shows in China presents a unique opportunity to directly engage with suppliers. Events such as the China International Textile Fabrics and Accessories Exhibition (Intertextile) and the China International Cotton Conference attract numerous suppliers from across the country. At these shows, importers can closely examine cotton cloth and yarn samples, discuss customization details face – to – face, and build strong relationships with suppliers. However, there are costs associated with participation. Travel expenses, including flights, accommodation, and local transportation, can amount to a significant sum. Entrance fees for these events can range from a few hundred to over a thousand dollars, depending on the event and the type of access required. If an importer plans to set up a booth to showcase their brand or requirements, additional costs will be incurred, which can start from several thousand dollars depending on the booth size and location within the exhibition venue. Setting up a booth can be a great way to attract the attention of potential suppliers and have more in – depth discussions about the specific requirements for custom – made cotton cloth and yarn.
1.3 Collaborating with Trade Agents
Trade agents in China can be invaluable partners in the sourcing process. They possess in – depth knowledge of the local market, established connections with suppliers, and can handle various aspects of the import process on behalf of the importer. Trade agents typically charge a commission, which is usually a percentage of the total order value. This percentage can range from 3% to 10% or even higher, depending on the complexity of the order and the services provided. Services may include supplier identification, negotiation, quality control, and logistics coordination. For instance, if an importer is new to the Chinese market and has limited knowledge of the industry, a trade agent can help identify reliable suppliers that meet their specific requirements, negotiate better prices, and ensure that the production process adheres to the importer’s quality standards. Trade agents can also help importers navigate the cultural and language barriers that may exist when dealing with Chinese suppliers, which is especially important when importing custom – made cotton cloth and yarn, as clear communication is crucial.
2. Communicating Customization Requirements and Requesting Quotes
2.1 Quality and Specification Selection
For custom – made cotton cloth and yarn, clear communication of quality and specification requirements is of utmost importance. Importers can provide the supplier with detailed information about the type of cotton (such as long – staple cotton, short – staple cotton), the thread count for yarn, the fabric weight and weave for cotton cloth, and any specific quality certifications they require. China offers a wide variety of cotton qualities, and the cost can vary significantly. For example, high – quality long – staple cotton yarn may cost around \(3 – \)5 per pound, while a lower – grade short – staple cotton yarn could cost around \(1 – \)2 per pound. For cotton cloth, a basic plain – weave cotton fabric may cost around \(2 – \)5 per yard, while a more complex weave or a higher – quality cotton blend could cost upwards of $10 or more per yard. If the importer has specific color requirements for the cotton cloth or if the yarn needs to meet certain strength or elasticity standards, it’s essential to communicate these clearly to the supplier.
2.2 Quantity and Delivery Time
The quantity of cotton cloth and yarn ordered will have a significant impact on the unit price. Generally, larger order quantities result in lower per – unit costs. However, custom – made products may require more time for production, regardless of the order size. When discussing delivery time with the supplier, it’s crucial to consider potential delays due to production capacity, raw material availability, or Chinese holidays. Rush orders may be possible, but they often come with additional costs. These additional costs could range from a 10% to 50% surcharge on the production cost, depending on the urgency and the supplier’s capacity. For example, if an importer needs a specific quantity of custom – made cotton cloth for a tight production schedule and the production timeline is short, the supplier may need to allocate additional resources to meet the deadline, which will be reflected in the price.
2.3 Quote Confirmation
Once all the necessary details have been provided, the supplier will generate a quote. The quote should include the cost of the raw materials, production labor (if applicable for custom – made products), any customization charges (such as special treatments for the cotton), packaging, and shipping (if applicable). It’s essential to carefully review the quote and clarify any ambiguous items. Some suppliers may offer a free initial quote, but if an importer requires multiple revisions or highly detailed quotes, they may charge a fee. This fee typically ranges from \(50 to \)500, depending on the complexity of the customization and the amount of work required to prepare the quote. For example, if the importer changes the quality or specification requirements multiple times or needs a detailed breakdown of costs for different cotton grades, the supplier may levy an additional charge to cover the extra time and effort.
3. Contract Negotiation and Initiating Production
3.1 Contract Preparation and Execution
A well – drafted contract is essential to protect the interests of both the importer and the supplier. The contract should clearly define product specifications, quantity, price, delivery time, payment terms, quality standards, and any other relevant terms. It is advisable to consult a legal professional with expertise in international trade to review and prepare the contract. Legal fees for contract drafting and review can range from a few hundred to several thousand dollars, depending on the complexity of the contract and the lawyer’s experience. Once the contract is finalized, both parties will sign it, officially commencing the production process. The contract should also include clauses for handling disputes, returns, and warranties to ensure that both parties are protected in case of any unforeseen circumstances. For example, the contract could specify the process for handling returns in case the cotton cloth or yarn does not meet the agreed – upon quality standards, including who will be responsible for shipping costs in such cases.
3.2 Production Monitoring and Quality Control
During the production process, it’s crucial to monitor progress to ensure everything is proceeding as planned. Importers can request regular updates from the supplier, including production timelines, quality control reports, and photos of the work in progress. Some suppliers may charge a fee for more frequent and detailed progress reports. Additionally, it’s a good practice to arrange for a pre – production sample. The cost of a pre – production sample can range from \(30 to \)150 per sample, depending on the complexity of the product and the materials used. If an importer wants to conduct independent quality control inspections, they can hire a third – party inspection company. Inspection fees usually range from 1% to 5% of the total order value, depending on the scope of the inspection and the inspection company’s rates. Quality control for cotton cloth and yarn should include checks for fiber quality, thread strength, fabric integrity, and any specific quality requirements to ensure that it meets the importer’s standards and the expectations of the target market. For example, the inspection may check for any impurities in the cotton, uneven yarn thickness, or flaws in the fabric weave.
4. Shipping and Customs Clearance
4.1 Shipping Method Selection
There are several shipping options available for importing cotton cloth and yarn from China. Sea freight is a popular choice for large – volume orders as it is relatively cost – effective. However, it has a longer transit time, typically taking anywhere from 2 to 8 weeks, depending on the destination. The cost of sea freight is calculated based on the volume and weight of the shipment, as well as the distance. For a standard 20 – foot container (which can hold a significant quantity of cotton products), the cost can range from a few thousand to over ten thousand dollars. Air freight, on the other hand, offers a much faster transit time, usually within 1 to 3 days, but it is more expensive. Air freight costs are usually calculated per kilogram, and for a shipment of cotton cloth and yarn, it can cost anywhere from \(3 to \)15 per kilogram. Express courier services like DHL, FedEx, and UPS are also an option for smaller, urgent shipments, with costs varying based on weight and destination. When choosing a shipping method, importers need to consider factors such as the urgency of the order, the value of the cotton products, and the cost – effectiveness for their business. For example, if the importer needs the cotton yarn urgently for a high – priority production run, air freight may be the preferred option despite the higher cost.
4.2 Customs Clearance Procedures
Customs clearance can be a complex process. It involves preparing and submitting necessary documents such as the commercial invoice, packing list, bill of lading, and any relevant certificates (such as origin certificates). Customs duties and taxes are levied based on the value of the goods, the country of origin, and the product classification. The duty rate for cotton cloth and yarn can vary significantly depending on the destination country and the type of product. For example, in the European Union, the duty rate for cotton yarn can range from 5% to 15% or more, while for cotton cloth, it can range from 8% to 20% or more. To simplify the customs clearance process, many importers choose to work with customs brokers. Customs brokers charge a fee, which can range from a few hundred to several thousand dollars, depending on the complexity of the shipment and the services provided. Customs brokers can help ensure that all the necessary documents are in order, calculate the correct duties and taxes, and handle any customs – related issues that may arise during the clearance process. They can also keep importers updated on any changes in customs regulations that may affect the import of cotton cloth and yarn.
5. Other Service Items and Costs
5.1 Packaging and Labeling Services
If an importer requires custom packaging or specialized labeling for their cotton cloth and yarn, the supplier can usually provide these services. Packaging costs will depend on the type of packaging chosen. A simple bale or roll packaging for cotton yarn may cost only a few dollars per unit, while more elaborate packaging for cotton cloth, perhaps with protective wrapping and custom – printed labels, can cost upwards of $10 or more per unit. If the importer wants to add branding elements to the packaging or labeling, such as custom – printed logos or specific product information, additional costs will be incurred. For example, a brand – conscious importer may opt for high – quality packaging with their logo embossed on the wrapping material, which can significantly increase the packaging cost.
5.2 After – Sales Service
Some suppliers offer after – sales service, such as handling returns, exchanges, or addressing quality issues. The terms and availability of after – sales service can vary among suppliers. Some may offer a limited warranty period, during which they will replace defective products free of charge. However, there may be costs associated with shipping replacement items. It’s important to clarify the after – sales service policy with the supplier before placing an order. For example, if an importer receives a batch of cotton cloth with a manufacturing defect, the supplier should be clear about whether they will cover the cost of shipping a replacement batch or if the importer will be responsible for some or all of the shipping costs. Additionally, some suppliers may offer services such as technical support for using the cotton products, which can be beneficial for importers who may have specific questions about processing the cotton cloth or yarn.
6. Risk Management
6.1 Quality Risks
There is always a risk that the cotton cloth and yarn may not meet the specified quality standards. To mitigate this risk, clearly define the quality requirements in the contract and conduct regular quality inspections during the production process. Importers can also negotiate with the supplier to include a penalty clause in case of quality non – compliance. For example, if the cotton used is not of the agreed – upon quality or if the yarn has inconsistent thickness, the supplier may be required to pay a penalty or provide replacement products at a discounted rate. Additionally, importers can request detailed quality control reports from the supplier at each stage of the production process to ensure that the high – quality standards are being maintained.
6.2 Delivery Delays
Delivery delays can be caused by various factors, including production issues, shipping problems, or customs delays. To minimize the impact of delivery delays, build some buffer time into the planning and establish clear communication channels with the supplier and the shipping company. Consider purchasing shipping insurance to cover any losses due to delays. For instance, if a shipment is delayed and an importer misses a key production deadline or a sales opportunity, the shipping insurance can help compensate for the financial losses incurred. Importers can also work with the supplier to develop contingency plans in case of unexpected delays, such as having alternative production schedules or shipping routes.
6.3 Price Fluctuation Risks
The price of cotton as a raw material is subject to market fluctuations. To hedge against price fluctuation risks, importers can consider entering into long – term contracts with suppliers at fixed prices or using financial instruments such as futures contracts. However, these strategies may involve additional costs and require some financial expertise. For example, a long – term contract may require a higher upfront payment or a commitment to a minimum order quantity. Futures contracts also have associated fees and risks, as they are based on market speculation.
7. Conclusion
Importing custom – made cotton cloth and yarn from China can be a rewarding business venture, but it requires careful planning, research, and management. By following the steps outlined in this article, importers can navigate the complex process of sourcing, production, shipping, and customs clearance. Understanding the various service items and associated costs is crucial for making informed decisions and ensuring the success of the import business. Stay updated on changes in regulations, market trends, and technological advancements in the textile raw material industry to maintain a competitive edge in the global market.
Tags: China import, custom – made cotton cloth, cotton yarn, service items, costs, customs clearance